Ein Leben ohne Spiegel ist schon schwer vorstellbar, dieses Objekt ist so praktisch und notwendig. Im Laufe der Jahrhunderte hat sich die Herstellung von Spiegeln von einem fast magischen Akt zu einem gewöhnlichen Vorgang entwickelt.
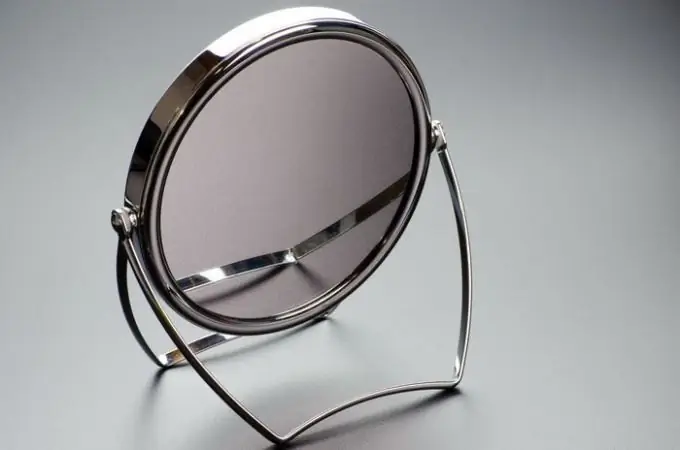
In der modernen Herstellung konventioneller Spiegel wird seit langem kein schädliches Quecksilber mehr verwendet, was den Spiegelhandwerkern viel Ärger bereitete. Statt Quecksilber wird heute Aluminium oder Silber verwendet. Das Mindestset für die Herstellung eines Spiegels ist eine glatte Glasscheibe, ein geeignetes Schleifmittel, demineralisiertes Wasser, Entfettungsmittel, eine Lösung aus Silbersalzen, Zinn, Chemikalien für den Aufarbeitungsprozess und Farbe für die Schutzschicht.
Seit der Antike ist die Reflexion mit magischen Eigenschaften ausgestattet.
Spiegelproduktionstechnologie
Die Glastafel wird über ein Förderband zum Schleif- und Waschplatz transportiert. Ceroxid (ein instabiles Metall aus Lanthaniden) wird als Schleifmittel zum Schleifen verwendet. Beide Seiten der Glasscheibe werden auf absolute Glätte gebracht, dann mit erhitztem destilliertem Wasser gewaschen, das die Fettverschmutzung auflöst.
Destilliertes Wasser ist gut, weil es keine Spuren auf dem Glas hinterlässt. Um problemlos eine reflektierende Schicht zu erzeugen, ist eine perfekt saubere Oberfläche erforderlich. Tatsache ist, dass die Wechselwirkung von Reagenzien mit Mineralien, die bei Verwendung von gewöhnlichem Wasser auf dem Glas verbleiben können, zu Defekten in der Spiegelbeschichtung führen kann.
Danach wird das Glas zum Versilbern vorbereitet. Silber kann sich nicht auf der Glasoberfläche festsetzen, daher wird eine dünne Schicht flüssiges Zinn auf eine polierte Glasscheibe gesprüht. Außerdem reagiert die Silbersalzlösung bei Zugabe der notwendigen Reagenzien mit dieser Zinnschicht.
Quecksilber war zunächst an der Herstellung von Spiegeln beteiligt, was das Leben der Handwerker erheblich verkürzte. Die Herstellung eines Spiegels dauerte durchschnittlich zwanzig Tage.
Auf der Glasscheibe, der reflektierenden Oberfläche, bildet sich ein dünner Film. Es ist weich, instabil, daher ist eine dichte Schutzschicht erforderlich. Auf Beschichtungsfehler geprüfte Bleche werden zur nächsten Stufe zugelassen.
Die letzte Phase der Spiegelherstellung
Weicher Silberfilm, der eigentlich ein Spiegel ist, erfordert einen guten Schutz. Kurzlebige Spiegel haben eine dicke Schicht Schutzlack auf der Rückseite. Für die Haltbarkeit wird eine dünne Kupferschicht auf das fertige Produkt gesprüht und bereits Farbe darauf aufgetragen. Die Trocknung von Lack und Kupfer erfolgt in mehreren Stufen bei unterschiedlichen Temperaturen. Nach vollständiger Trocknung werden die Spiegel erneut auf Fehler geprüft, wenn in diesem Stadium Bruchstücke mit Blasen oder dunklen Punkten gefunden werden, werden diese abgeschnitten.